Does it pay off to lock down the drains in a restaurant?
The article below was originally published in the Facilitator : December/January 2022 issue.
On Lockdown
The true value of preventing plumbing-related restaurant closures with Shawn Coe, CRFP, Panda Restaurant Group
What is your current title? How long have you been with Panda Restaurant Group?
My current title is regional facility manager. I have been with Panda Restaurant Group for approximately 2.5 years.
What is your history in the restaurant industry?
I have been in the restaurant business for much of my life. My restaurant experience began in operations, and I’ve held every position from dishwasher to area director. Now in my current role I am able to support operations, having walked a mile in their shoes.
How is facilities organized at Panda? How many locations do you have?
Our Restaurant Development Department consists of four sub-departments, with real estate, design, construction and facilities. Panda Facilities is structured with directors, senior facilities managers, regional facilities managers, associate facilities mangers and support team. Team members are located throughout the country, living in a home region and supporting two or more regions with anywhere from 100 to 200 stores. I support close to 150 locations and several different concepts (Panda Express, Panda Inn, Uncle Tetsu, Ippudo and Yakiya). While the number may seem high as an FM, I am supported by our facilities support team and a number of in-house departments, and we utilize CMMS software to manage our work order process.
There are few items that could potentially shut down your restaurants like having no utilities, hot water or plumbing. What programs do you have in place to minimize plumbing issues?
Store shutdowns are something that we work hard to minimize. For hot water issues, we have implemented redundant tankless hot water heater systems. As for plumbing backups, we have been testing locking drain covers for the past two years with a goal of proactively preventing drain back-ups on the main sewer line.
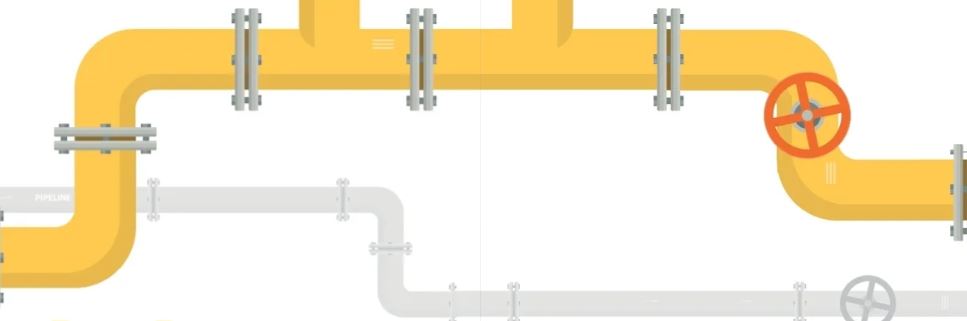
What prompted the test of drain lock covers?
When I began working with Panda, I was supporting the West Los Angeles Region and noticed that I was having excessive drain back-ups. The stores in this region are older and tend to have more build-up. While we did have stores receiving regular drain jetting, the plumbers would still be pulling foreign objects out of the drains.
How many restaurants were chosen? How were the locations determined?
We partnered with operations to select 10 stores. It’s simple to pick just the opportunity stores, as we know these are the exceptions. Our thought process was to include a broad spectrum of stores: old, new, opportunity, drive-thru and end-cap locations. In the end with the 10-store test, we were able to get data from stores that represents our entire brand.
Can you share the pre-test plumbing R&M costs, on the average, for these restaurants?
The monthly plumbing drain back-up average spend over a two-year pre-install was $93.59 per store. The average cost was $267 to clear the back-up on the main grease line. The numbers do not include any sanitary line back-ups.
What was the approximate cost per store for the covers? Was there any prep work required for the drains?
The cost to implement the locking drain cover project was $950 per store. Locking drain covers were roughly $400 per store, depending on the number of drain locks needed to cover every floor sink, trench drain and three comp sink. To prep the stores, we contracted with our vendor to drain jet the main grease line to include the outline after the grease trap, mini-jet the branch lines and install the drain locks.
Who kept possession of the keys for the locking drain covers?
We decided to not give the security Torx bit to the stores, which would prevent the stores from removing the drain covers. In addition, I notified my plumbing vendors that the floor sinks would now have the drain locks and to ensure that all of their techs came prepared to service with a Torx bit.
Do you have line-jetting preventive maintenance programs in your restaurants? If so, what is the frequency of the jetting?
Our stores do have drain jetting service. Depending on the area, it can be one to three times per year. This preventive maintenance approach helps to maintain the integrity of our plumbing lines.
Where were the drains located? Approximately how many per store were included?
The drains included every floor sink, mop sink, trench drain and, in some stores, the three comp sink drains. While I believe the mop sink to be a major contributor to the drain back-ups, it was important to secure any opening. Our stores already had floor screens for each floor sink, along with a secondary removable drain cover. At first glance, that is a great practice and should prevent foreign material down the drains. Going to the store late at night or early in the morning, I noticed both would be removed to allow cleaning of the floor sink and floor screen. It’s a great sanitary practice in cleaning; unfortunately this is the root cause of the drain back-ups. I definitely saw the need to provide a solution that couldn’t be removed.
What were the goals for this test?
The goal of the test was simple: to reduce drain back-ups emergencies.
During the two-year test, did you provide periodic reporting on the results?
I provided updates to the stores, leadership team and department at the three-month, six-month, nine-month, one-year and two-year mark. I recall reviewing the numbers at the one-year mark, and the spend for the stores was roughly the same. I was including the cost to purchase and jet the lines in my figure. I was hoping for more positive numbers to share with a new region I was supporting. The regional director of operations challenged me on a call, stating that my numbers were incorrect. I didn’t understand at first, as I was attempting to defend the black-and-white numbers in front of me. Then, I realized that the results of this program don’t only show up on the R&M line on our P&L. Any store shut down impacts the store on their sales line, food cost and labor line. The regional director of operations, his leadership team and I were able to come up with a formula to discover the true value of a shut down:
Sales loss = Average response time for plumbing emergency x average sales per hour
Labor loss = Average response time for plumbing emergency + reopening time x average associates on shift x average wage
Food costs = Costs of all food on steam table (as we have to discard)
True costs = Sales loss + labor costs + food costs + plumbing costs
What were the results of the test in regard to plumbing R&M and store shutdowns?
After two years of running the test and utilizing the true costs value, I can really say this program was a success. Our actual drain back-ups and shutdowns were reduced by 59.63%. When we factor the savings of the true costs, these 10 test stores were saving in the tens of thousands each year. There is an additional cost saving not discussed that should be considered an added benefit with the project: When technicians snake/cable our lines, eventually it will ultimately lead to a broken P-trap. We then have a larger spend on getting a night crew to dig up the floor sink and P-trap, and complete tile work. Fewer back-ups reduces this risk.
What are the next steps you would like to implement?
We have many ideas on how to proceed with this project. One will be to present this data with our Construction Department and have the locking drain covers added for all new store openings. While we began our testing with 10 stores, our ops leadership partners have seen the benefits and requested additional stores. Currently we have roughly 50 stores with locking drain covers. My next goal will be to expand testing to an entire region. Shawn Coe’s restaurant career began in 1987. He has been employed by smaller chain restaurants in a variety of positions, from dishwasher to area director. His operational background, along with military experience as a C-5 crew chief, has helped him transition to working as a facility manager with Panda Restaurant Group. He supports Panda Inn, Panda Express, Uncle Tetsu, Ippudo, Hibachi San and Yakiya.
Visit Drain-Tech.com to shop Drain Locks
Health Department Inspections
Health Departments are now deducting major points for drain backups and fruit flies. Many health inspection reports are now being published online (such as the one below) and even on review sites such as Yelp and Trip Advisor. It is too costly to ignore these problems.
Drain-Net has developed the most extensive product portfolio to help your restaurant tackle these problems head on. Take a look at our website and give us a call at (908) 236-0277 if you need help finding the right solutions.
We also offered a new line of compounds that fight fruit flies in all their various locations. Check out our Drain DEFENDER line of products here.
One Product – Many Names
Drain-Net has developed a highly popular waste interceptor product line we call GDRU’s. However, this commercial kitchen necessity can be called many things.
We call it a GDRU (Garbage Disposal Replacement Unit) because it can replace mechanical garbage disposals which have been outlawed in a number of states. Instead of grinding the food waste and wasting precious freshwater for flushing, the strainer-drawer in GDRU strains solid particles under the pre-rinse sink when dirty dishes are being pre-rinsed, affecting a much needed pretreatment process of restaurant wastewater.
A GDRU can also be called an “Indirect Waste Interceptor”.
Many states such as New York and New Jersey have passed laws that require restaurants to install indirect waste units. A typical plumbing code states, “Indirect waste connections shall be provided for drains, overflows, or relief vents from the water supply system, and no piping or equipment carrying wastes or producing wastes or other discharges under pressure shall be directly connected to any part of the drainage system.” Our versatile GDRU’s can easily be installed to meet this requirement. An air gap can be created before the inlet or after the outlet to meet the indirect connection requirement.
A GDRU can also be called a “Grease Trap Pre-Strainer.”
Grease Traps and Grease Interceptors primary function is to separate grease from wastewater. However, debris filled water can quickly accumulate in a grease trap, rendering it ineffective. A GDRU should be installed before waste water reaches a grease trap. Commercial kitchens who install Garbage Disposal Replacement Units see a dramatic improvement in grease trap functionality and can reduce grease trap service visits.
Believe it or not a GDRU can go by even more names such as an “Indirect Waste Separator,” “Food Waste Separator,” “Flat Strainer,” “Indirect liquid waste separator,” or a “Wet Waste Interceptor. Whatever you call the product, you can be sure that your restaurant or commercial kitchen will stay compliant with local plumbing codes and that your drains stay free of food waste.
Click here to view our Garbage Disposal Replacement Unit product line
Strainer Basket to protect floor sinks from small particles
Floor drains can be a life-saver in many areas of a restaurant, as numerous pieces of commercial kitchen equipment require a drain to prevent water from leaking all over the floor, creating a potentially hazardous workspace. However, Drain-Net has provided an answer to this issue with its 8 1/2” x 8 1/2” Stainless Steel Floor Drain Strainers (SLF-10). These drain strainers will allow water to flow freely into the drain while stopping the material that may otherwise clog the drain from getting into the plumbing, saving your business from additional maintenance costs and pipe repairs.
This drain strainer basket is a 7 1/2″ square so that it fits 8 1/2″ floor sinks. It is 2″ tall. It has an 11″ flange with handles for easy removal. The fine mesh is ideal for straining small particles such as rice and seeds.
We have a new online sales price for these strainer baskets. Purchase it today!
The Floor Drain Brush Comparison: Drain-Net vs. Carlisle Flo-Pac
Carlisle Drain Brush Problem: Can’t clean curved piping.
Drain-Net Brush Solutions: Made of durable twist wire to provide strength and “bendability” to clean curved piping. Also features a poly ball on the end to guide smoothly through elbow turns in drain pipes.
Carlisle Drain Brush Problem: The brush head falls off, getting stuck in the drain
Drain-Net Brush Solutions: The brush head and handle are one unit so the brush head can’t fall off.
Carlisle Drain Brush Problem: While cleaning the drain, nasty drain junk splashes on you
Drain-Net Brush Solutions: Splash guard covers drain while cleaning so you stay clean!
Carlisle Drain Brush Problem: You have to buy different brush head for each drain size.
Drain-Net Brush Solutions: One size fits 2″, 3″, and 4″ drain sizes.
Hard to reach floor sinks – NO PROBLEM!
Every floor sink needs to have a strainer basket to keep food, trash, and debris out of their floor sink drains. However, sometimes these floor sinks are hard to reach, making it difficult to empty and maintain. Drain-Net has solved this problem with the Extedo-Net. Drain-Net can add an extending handle to any floor sink basket for easy installation and removal. Choose the length you need (standard sizes includ 1,2,3, and 4 feet long). Get yours today!
Top 10 Benefits for Preventative Plumbing at Your Restaurant
1. Fewer plumbing expenses because preventing drain clogs also mean less calls to a plumber for emergency repairs and drain line jetting.
2. Prevent wet floors which are a common cause for slip and fall accidents. Restaurant owners decrease their liability and increase employee safety.
3. Reduced risk of expensive repairs to piping and sewer lines which can result when bags, rags, large seeds, and other solid waste clog grease traps and pipes.
4. Increase efficiency of grease trap do to reduced debris.
5. Lower risk to city fines for violating wastewater discharge compliance standards
6. Reduce or eliminate drain flies which are attracted to the “gross stuff” that builds up in drains when not maintained.
7. Increased employee productivity when they don’t have to handle flooded floors and emergency drain backups.
8. Decreased frequency of grease trap servicing/pumping due to reduced solid waste in grease trap.
9. Eliminate the need for chemical pipe cleaners which can be very harmful to the environment and dangerous for employees to handle.
10. Reduce or eliminate repulsive odors that can occur when debris builds up inside of drain lines.
Free Drain Evaluation for Restaurants in NY, NJ, and PA
Is your restaurant, commercial kitchen, or facility experiencing drain and plumbing related issues? Are you interested in preventative plumbing solutions, but aren’t sure what you need or what will work for you? We want to help!
Drain-Net is now offering FREE Drain Evaluations for your facility. We will visit your facility and identify problem areas for drains and provide you with preventative plumbing solutions and a quote so you can calculate your ROI. There is no hassle, cost, or obligation.
Currently the Free Drain Evaluations are being offered in the New Jersey, New York, and Eastern Pennsylvania region.
How do I get a free Drain-Evaluation?
Call 908-236-0277 or visit www.drain-evaluation.com
RFMA 2012 is for all Restaurant Facility Professionals
There’s no point in denying it, times are tough and budgets are tight. You may be thinking that you don’t have money in the budget to attend a Restaurant Facility Conference. However, if you attend RFMA 2012, presented by the Restaurant Facility Management Association March 4-6, 2012, you will reap valuable benefits throughout the year from the tools you take away and put into practice. Drain-Net is proud to be one of many great companies that have innovative ideas to help your restaurant reduce maintenance costs and operate more efficiently.
It is the ONLY event of its kind that is developed exclusively for restaurant facility management professionals. The conference will enable you to attend a number of education sessions that are directly applicable to your work and will allow you to network with a variety of restaurant facility management colleagues from around the country. ALL of the presentations are tailored to the restaurant facility management industry and give information on how to improve your technical knowledge needed to maintain and repair restaurants and commercial kitchens, how to find cost-saving alternatives to our current practices.
Here are some more details:
The RFMA 2012 Annual Conference is open to Restaurant Facility Professionals who can attend as association members or non-members.
Dates: March 4-6, 2012
Location: The Mirage in Las Vegas, NV
Where to register: http://www.rfmaannualconference.com/registration.cfm
Drain-Net’s Booth: 309
Drain-Net is proud to sponsor the Opening Party!
Pre-Strainers: The Key to a working Grease Trap!
Did you know that as solid waste collects in your grease trap the capacity is diminished, decreasing its ability to separate and capture grease, even to the point of complete ineffectiveness? The best product to keep your grease trap operating correctly is a Grease Trap Pre-Strainer.
One of the primary causes of drain clogging and backflow in restaurants is the waste and debris that comes from food preparation and ware-washing sinks. These grease trap pre-strainers intercept 98% of solid particles from wastewater before they reach your drains, grease trap, and facility piping. Features of the Grease Trap Pre-Strainer include:
- Removable tray allows user to empty solids into a trash receptacle in seconds
- One unit can handle multiple sinks (up to 18 gallons per minute)
- Adjustable height for easy installation
- 2” connection from either side
- Durable stainless steel construction
Click here to view Drain-Net’s full product line of Grease Trap Pre-Strainers.